Encoders Feature Article
Encoders Special Feature
- Chapter 1
- What is an encoder?
1. Outline
An encoder is a sensor that detects changes in mechanical position and directions / angles, converts them into electrical signals, and outputs them. The name of the encoder is derived from "encode", which means that the angle and position displacement are coded, that is,
An encoder is a sensor that detects changes in mechanical position and directions / angles, converts them into electrical signals, and outputs them. The name of the encoder is derived from "encode", which means that the angle and position displacement are coded, that is,
Furthermore, there are two types of rotary encoders, incremental type and absolute type. The incremental type outputs a signal according to the amount of rotation, and the absolute type outputs a signal at the absolute position of rotation.
- - Contents -
- 1. What is an encoder?
- (1) Outline
- (2) Operating principles
- ・Optical rotary encoders
- ・Magnetic rotary encoders
- ・Incremental
- 2. Introduction of our encoders
- (1) Milestones
- (2) Features and strengths
- (3) Applications
2. Operating principles
Rotary encoders include optical and magnetic encoders. The optical encoder senses the luminous flux from the light emitting element with the light receiving element through slits carved at equal intervals in the rotating disk and the fixed disk. The optical signal sensed by this light receiving element is converted into an electric signal and output as an approximate sine wave or square wave.
In addition, there are two types of optical encoders: transmissive type and reflective type.
Optical rotary encoders
Ⅰ. 透過型ロータリエンコーダ
Ⅰ. Transmissive type
In the transmissive type, the light receiving element detects whether or not the luminous flux from the light emitting element has passed through the slit of the rotating disk. The number of slits corresponding to the resolution of this rotating disc is radially opened.
Ⅱ. Reflective type
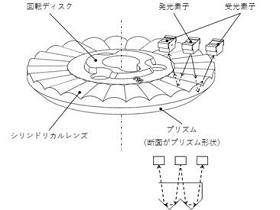
The reflective type is a method in which the luminous flux from the light emitting element is reflected by a rotating disk consisting of a cylindrical lens and a prism and sensed by the light receiving element, which facilitates miniaturization of the product. These optical types have the features of high accuracy and high resolution, and are not easily affected by magnetic fields. In addition, there is a coupled encoder that is an evolution of the reflective type. This uses a transparent resin molded part (roof prism) consisting of an aspherical lens and a prism. The light emitting element and the light receiving element are mounted on the same substrate, and the roof prism is fixed on the opposite side of the rotating slit. The roof prism forms a slit image illuminated by the light emitting element on the light receiving element side. This image is imaged on the same plane as the rotating slit and works like a fixed slit in a normal encoder. Also, the image rotates in the opposite direction as the rotation slit rotates. Then, when the slit of the rotating slit and the image of the formed slit overlap, the light receiving element detects the optical signal.
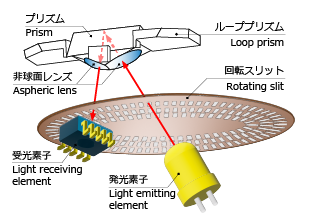
Magnetic rotary encoders
The magnetic encoder detects changes in the magnetic poles of a rotating disk with N and S poles magnetized alternately on the outer circumference by a magnetoresistive element (MR element), converts it into an electrical signal, and outputs it as a square wave. Its features are small size and light weight, and there is no light emitting element, so the power consumption is smaller than that of the optical type.
Incremental
Incremental type rotary encoders have A-phase, B-phase, and Z-phase outputs. The A-phase output represents the rotation angle of the shaft before and after operation. Phase B is a signal with a certain phase difference from phase A and is used to detect the direction of rotation of the shaft. (Specifically, the direction of rotation is usually detected by the signal level of phase A at the pulse edge of phase B.)
The Z phase is a signal that outputs only one pulse per rotation of the shaft, and is used as a reset signal and start signal. In our rotary encoder, when the shaft is rotated by CW, there is only one rise of phase B while the Z phase is “1 (High)”. Therefore, the ideal reference position output is obtained by taking the rising "AND" of the Z phase and the B phase during CW rotation. (Descent of Z phase and B phase at CCW rotation)
- Chapter 2
- Introduction of our encoders
1. Milestones
In the past, our encoder business was marketed and sold by us, and designed and manufactured by Nidec Copal Corp. In January 2019, we took over the designs and manufactures from the company and achieved the complete commercialization of manufacturing and sales. Therefore, we are aggressively taking on the challenge of the new field of position sensing, including potentiometers, which contributes to the expansion of the sensing business.
1979 | Developed optical rotary encoders RE20 for tape speed control of magnetic recording device | Developed optical rotary encoders RE20 for tape speed control of magnetic recording device |
---|---|---|
1986 | 1986 | Released rotary encoders RES20 for setting and rotary encoders with panel waterproof, REW45 |
1988 | Released rotary encoders RE30D with square wave output | Released rotary encoders RE30D with square wave output |
1989 | 1989 | Released rotary encoders with click REC20 |
2015 | Released Joystick encoders CJ25 | Released Joystick encoders CJ25 |
2019 | 2019 | Acquired designs and manufactures of potentiometer and encoder business from Nidec Copal [*Full business of manufacturing and sales] |
2. Features and strengths
Our encoders specialize in incremental type small rotary encoders.
The rotary encoder for setting is available in magnetic type as well as optical type, and we have a wide variety of products according to the customer's usage such as with / without switch, with / without click, and panel waterproof type. Rotary encoders for servos are available in optical sizes from φ12 mm to φ30 mm, and are characterized by their small size and light weight, and we have a lineup from low-cost types to high-resolution products.
Joystick encoders
In addition, we would like to introduce the joystick encoder as a unique product. It is a multifunctional device equipped with an optical encoder and push switch on the joystick, and boasts a long life of 500,000 times for the joystick and 1 million times for the encoder and push switch.
Multi-function device, Excellent operation feeling
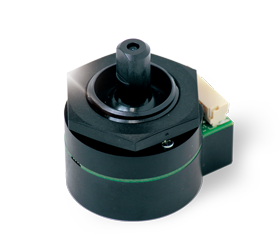
-
Joystick, optical encoder, and push switch functions in one package
-
Suitable size for panels. Smooth operational feel
-
Long life: Joystick 500,000 cycles, encoder and switch 1 million cycles
Functions
Joystick | Encoder | Switch |
---|---|---|
4 or 8 directions
|
20 positions (5 P/R)
|
Push-on
|
![]() |
![]() |
![]() |
3. Applications
Our encoders are ideal for the following applications. It's recommended, so please consider it.
Medical equipment
Measuring instrument
Communication base Sta.
Broadcast equipment (Mixing console)
Ticket-vending machine
ATM