Für LiDAR Polygonspiegel und Scannermotoren Vol.2
Für LiDAR Polygonspiegel und Scannermotoren Vol.2
Kapitel 7
What is a Reflectivity?
The most important spec in a polygon mirror is what is called “Reflectivity”.
The reflectivity is the percentage of a beam emitted from a laser diode bounces off when reflected by a polygon mirror. For example, a polygon mirror with a reflectivity of 95% is one that has a 95% ability to reflect and scan the emitted beams (100%).
LiDAR detects lengthwise and landscape
In a somey technically, the LiDAR scans horizontally and vertically.
To do this, need a polygon mirror to scan the horizontal X-axis and a mirror to scan the vertical Y-axis. At first, the laser beams emitted by the laser diode are reflected in the polygon mirror that scans in the X-axis, and then the horizontally scanned beams are reflected in the mirror that scans in the Y-axis. Assuming the reflectivity of these mirrors are 95%, the laser diode: 100% ⇒ X-axis: 95% ⇒ Y-axis: 90.25%.
Reflectivity also varies with objects
The beam reflected in the mirror reflects back to the object. For example, suppose you XY scan a black object with the mirror with the 95% reflectivity described above. The black object has a reflectivity of only about 5%. At emitting the beams from the laser diode: 100% ⇒ at the X-axis scan: 95% ⇒ at the Y-axis scan: 90.25% ⇒ the black object's reflectivity: 5% ⇒ at final return rate: 4.5%, which means that 100% of the beam returns only 4.5%. Considering its circumstances, the accuracy of the photodiode and the correction by software are also important.
The higher the reflectivity, the better
Polygon LiDAR is critical to reducing the loss of beams emitted by the laser diode. The higher the reflectivity of the mirror, the better. It is also important that the reflectivity varies less with angle.
Our technology development
Gold-plating is the most versatile method for making polygon mirrors with high reflectivity and low dispersion. However, gold-plated mirrors are so expensive that their feasibility is very low when considering mass production. Therefore, we have developed multi-layer di-electric polygon mirrors that satisfy the three requirements of high reflectivity, low dispersion and reasonable price.
Multi-Layer di-electric coating reflectivity test data
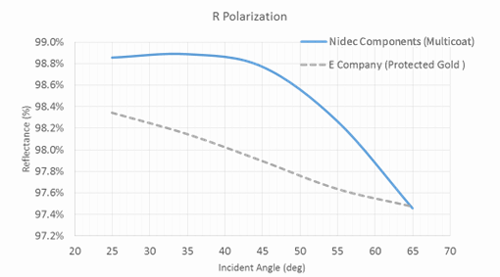
- NIDEC COMPONENTS' excellent aluminum cutting technology achieves high flatness and surface smoothness that cannot be achieved by resin at all.
- NIDEC COMPONENTS’ multi-layer di-electric coating will not only achieve low cost but will have reflectivity levels equivalent if not better than gold.